A turnaround is defined by American Petroleum Institute as: “A planned, periodic shutdown (total or partial) of a process unit or plant to perform maintenance, overhaul and repair operations and to inspect, test and replace process materials and equipment.”
Many industries view turnarounds as an inevitable and necessary evil and accept that they would “cost what they cost” and “take as long as they take”. However, if poorly managed, turnarounds offer significant risk of production disruption due to leaks and other production trips.
Proper preparation will make the difference between a successful turnaround and a failure. While turnarounds are so critical to a plant reliability, and therefore the company’s profitability, it is amazing how many difficulties organizations have in planning and executing them properly.
Top 5 reasons and facts
According to Construction Industry Institute (CII), there are 5 main reasons why turnarounds fail, and 5 facts related to them:
1 Not obtaining timely, complete and coherent planning and control
Over 80% of turnarounds experience cost overruns
2 Not obtaining objective, timely, complete and coherent information
90% report scope growth from 10% to 50%
3 Poor management of historical data due to outdated tracking tools
Cost control and forecasting is implemented on less than 20% of all turnarounds
4 Poor management coordination and no adequate communication concerning the relevant information in a timely, constant and efficient manner to the entire turnaround organization.
Approximately 50% of turnarounds suffer schedule delays
5 No integration of the contractor organization in the turnaround organization
Unplanned additions cost 30%-50% more than planned work
Based on our expertise in serving different industries for more than 25 years in turnaround and project controls, we have defined the key items for success that can help you overcome turnaround failures:
Key items for successful turnarounds
- Integrated turnaround teams (client – contractor – subcontractors)
- Management by performance indicators
- Adequate planning and control in the pre-execution phase
- Strict scope management
- Total budget approach (Maintenance/ Projects/ Start-Stop/ Production loss)
- Historical data
- Adequate software tools
Get back in control with Turnaround Management and Control Course
Tackling all key items above and being back in control is possible by learning from the experts who could bring you their skills and knowledge from the field to help implement the industry’s best practices. The Turnaround Management & Control course of the Cost Engineering Academy is a modern training that could keep you up-to-date with today’s best practices.
The course is split into two parts of each two days. Part one walks you through the phases and processes of a turnaround, following the Total Turnaround Management approach. You will learn how to plan for cost, time, safety and quality, and prevent common pitfalls. Interactive discussions and case studies are part of this.
The second part is about all aspects of turnaround project controls where all elements of total turnaround cost management are covered:
- Turnaround economics
- Budgeting and estimating
- Contracting and tendering
- Planning and scheduling
- Progress, cost control & earned value analysis
- Change management
- Close-out and benchmarking
Do you want to know more about the Total Turnaround Management Solution Cleopatra Enterprise? Please feel free to contact our experts.
Turnaround Progress & Cost Control: Why Digitalization is a must
Upcoming Webinar
Join our upcoming webinar on the 18th of August to learn how a Digital Progress & Cost Control system can help you maximize the turnaround performance and minimize the manual efforts by tracking your turnaround costs via interactive dashboards, cost reports, graphs and KPIs.
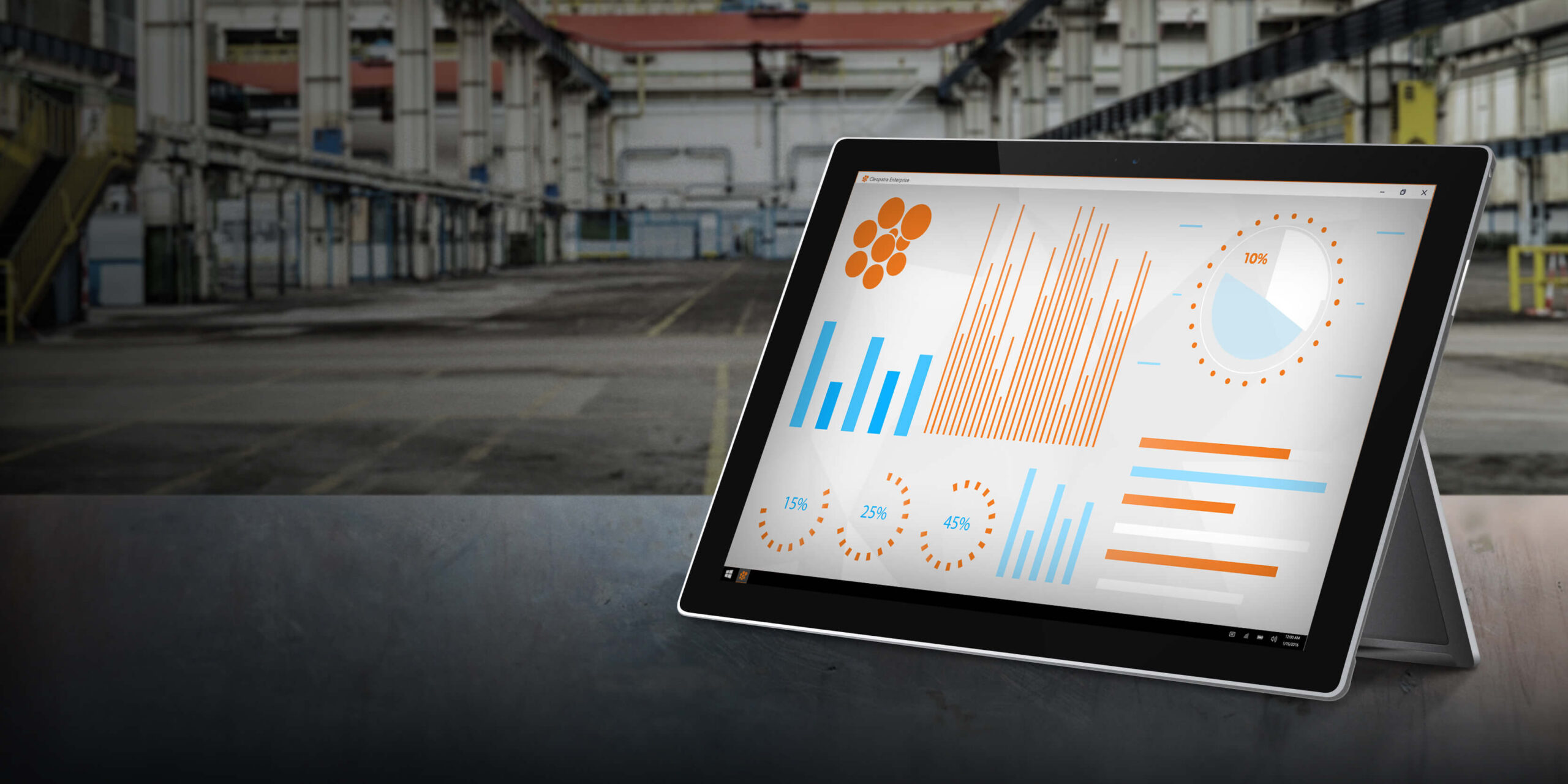